What does aluminum alloy belong to?
Aluminum alloy is a non-ferrous metal structural material.
Aluminum has low density, but high strength, close to or surpassing high-quality steel, good plasticity, and can be processed into various profiles. It has excellent electrical conductivity, thermal conductivity, corrosion resistance and other properties. It is widely used in industry and is second only to steel. Through heat treatment, some aluminum alloys can obtain better mechanical properties, physical properties and corrosion resistance.
Hard aluminum alloy belongs to AI-Cu-Mg system, usually contains a small amount of Mn, and can be strengthened by heat treatment. It is characterized by high hardness but poor plasticity. Super hard aluminum is Al-Cu-Mg-Zn system, which can be strengthened by heat treatment. It is an aluminum alloy with high strength at room temperature, but it has poor corrosion resistance and fast softening at high temperature.
Forged aluminum alloys are mainly Al-Zn-Mg-Si alloys. Although there are many types of added elements, the content is small, so they have good thermoplasticity and are suitable for forging, so they are also called forged aluminum alloys.
Aluminum alloy processing
What kinds of aluminum alloy processing technology are there?
1. Sandblasting is also called shot peening.
Cleans and roughens metal surfaces with the impact of high-speed sand flow. Using this method for surface treatment of aluminum parts can make the surface of the workpiece have a certain degree of cleanliness and different roughness, thereby improving the mechanical properties of the surface of the workpiece, thereby improving the fatigue resistance of the workpiece and increasing the bonding strength between the coating and the coating. , extending the durability of the coating film, but also conducive to the leveling and decoration of the coating. This aluminum machining process is often seen in various Apple products and is increasingly used in existing TV casings or frames.
2. Polished.
Using mechanical, chemical or electrochemical methods to reduce the surface roughness of automobile aluminum parts and obtain a bright and smooth surface. Grinding process is divided into: mechanical polishing, chemical polishing, electrolytic polishing. The aluminum parts of the car can be close to the mirror effect of stainless steel after mechanical polishing + electrolytic polishing, giving people a high-end, simple, fashionable and avant-garde feeling (of course, it is easy to leave fingerprints and needs to be taken care of).
3. Brushed.
Metal wire drawing is a manufacturing process in which the aluminum plate is repeatedly scraped out of the line with sandpaper. There are several different drawing methods such as straight grain, miscellaneous grain, spiral pattern and silk thread. Metalworking WeChat, the content is good, it is worth paying attention to. The metal wire drawing process can clearly reveal every filament, so that the metal matte shines with a filament luster, and the product has a sense of fashion and technology.
4. High gloss cutting.
Use the engraving machine to reinforce the diamond knife on the main shaft of the engraving machine rotating at a high speed (generally 20,000 rpm) to cut the parts, so that the surface of the product produces a local high-gloss area. The speed of the drill bit has a great influence on the cutting gloss.
5. Anodizing.
Anodic oxidation refers to the electrochemical oxidation of metals or alloys. Under the corresponding electrolyte and specific process conditions, an oxide film is formed on the surface of aluminum products (anode), and there are certain process conditions. Anodizing can not only solve the defects of aluminum surface hardness and wear resistance, but also prolong the service life of aluminum and improve its aesthetics. It has become an indispensable part of aluminum surface treatment, and it is also widely used and successful. craft.
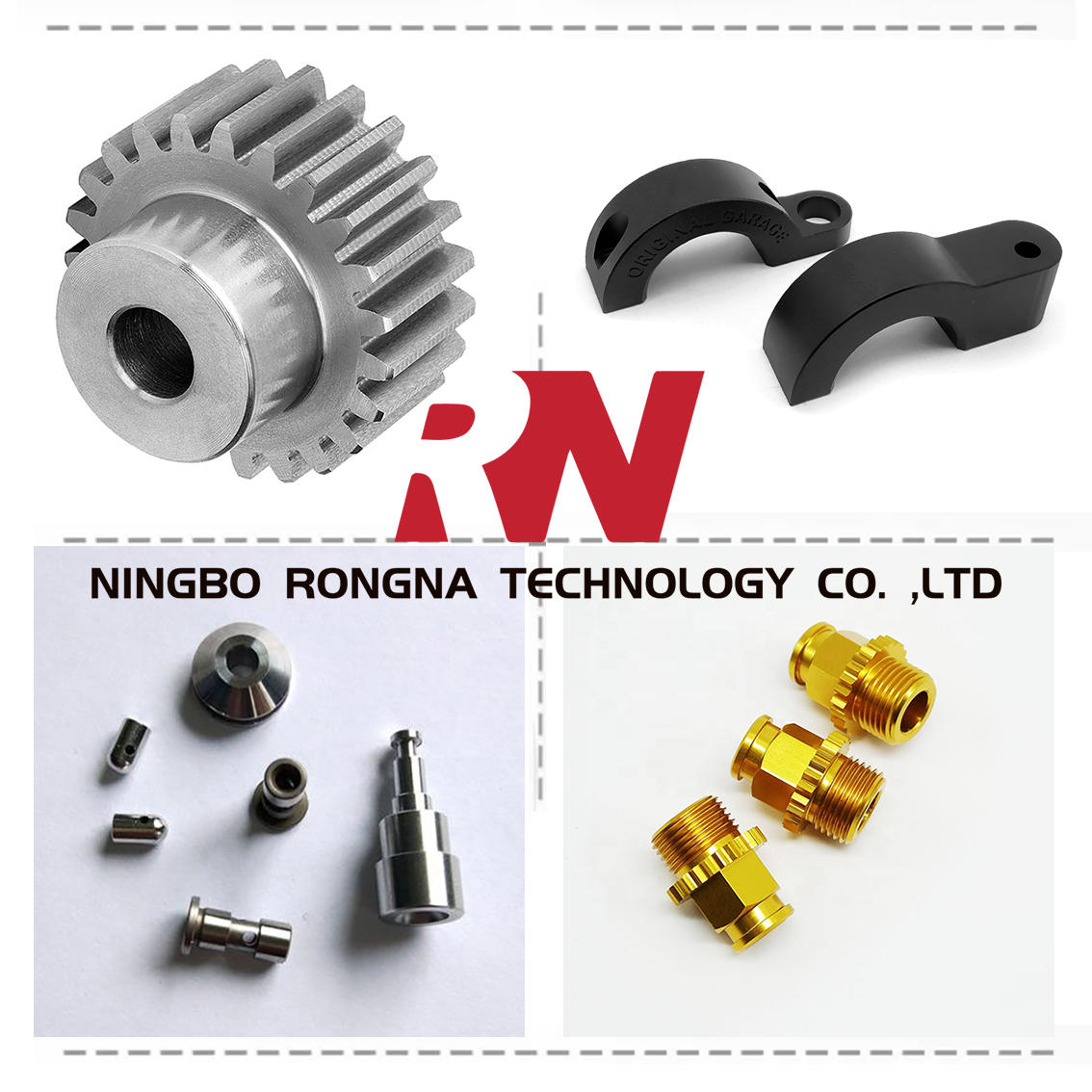